The retail landscape is constantly evolving, and it’s never been more important than ever for businesses to build a network of happy and loyal customers. Unfortunately, in a world filled with viral marketing campaigns and flashy Instagram posts, it’s easy to forget about the basic processes in a business that truly delight your customers.
The pick and pack style of each business will greatly vary depending on business size, customer demand, and the variety of products being sold, but the one unchanging variable is that your order picking method has a direct impact on how quickly your customers will receive their items.
In this post, we take a look at a few of the picking methods businesses of different sizes utilise, while also giving you a few tips to keep in mind when you’re thinking about switching up the way you pick your customer orders.
Discrete Order Picking
If you’re a small business owner and you’re looking to do things as deliberately and accurately as possible, then you probably employ the discrete order picking methodology.
This method is very good for alleviating the ensuing anxiety that arises with pick errors, and if you utilise this method you’ll most likely be collecting the items for each order before moving onto the next. This is technically the easiest way for new businesses to start picking and its simple methodology makes it really effective at avoiding picking errors.
A lot of small businesses start off with discrete order picking because it’s risk-free and safe. The underlying concept behind it stems from an old proverb “if you chase two rabbits, you will catch neither one”, meaning it’s better to focus on one thing at a time because doing more than that will result in inferior outcomes.
Although great for accuracy, discrete order picking falls short when it comes to efficiency. Under this method, the travel time for each order can only ever be as good as the distance of the items to the actual packing area.
Should you use discrete order picking?
Use this method if you’re just starting out and you’re just getting into the hang of picking and packing. Don’t use this method if you’re starting to grow and you’ve noticed an increase in the time spent picking orders.
Batch Picking
So you’ve probably heard of meal prepping; a fitness craze that hit Instagram a few years ago where health enthusiasts would post high-resolution images of batch prepped meals in storage containers with #mealprepmonday.
You might be wondering what this method of picking has to do with chopping veggies, but there is a method to our madness. You’ll be utilising batch picking if you focus on picking SKUs rather than each individual order.
This is a great way to save time if you have a conservative range of SKUs and a high volume of orders. Companies who use this method typically organise their batches by size or cubic volume and then they define how many items/orders a batch should constitute.
Batch picking helps you fulfil orders really quickly, but you’ll need to be using an order management system (OMS) that will help you arrange orders in a picking sequence. If you’re unsure whether or not you fall into this category, it might be worth assessing whether you need to be. If you’re currently looking into whether or not you need an OMS, these might be some issues you’re currently facing:
- You’re looking to reduce the amount of time spent searching for information on items
- You’re manually printing labels, invoices and notifying customers
- You’re experiencing an influx of complaints from customers who’ve received the wrong orders
- You’re unsure of how much inventory you have.
Batch picking is one of the most efficient ways to pick orders because you can pick multiple orders at the same time, one SKU at a time. However, there are technology prerequisites for this method meaning if you’re currently using it, you’re pretty pro at eCommerce fulfilment.
Should you use batch picking?
Use this method if you have a warehouse management system (WMS) to help you organise orders into batches, and it’s also really great if you have a lot of small items that can fit easily into your picking carts. Don’t use this method if you need to pick really bulky items.
Wave Picking
If you’re a level up from batch picking, you’ll probably start noticing that collecting SKUs in batches is creating a lot of pick-cart traffic which makes is really hard to sort the items for packing.
As your business grows in both size and product offering, eventually you’ll have so many SKUs in your inventory that it would be inefficient to continue picking in batches according to individual items.
If you’re currently picking in waves, then you should understand what short-interval scheduling is, but for those who aren’t sure this is a method where groups of similar orders are released in ‘waves’ throughout the day by a warehouse management system (WMS).
If you’re unfamiliar with what a WMS should do, here’s a great presentation that will take you through the basics:
The aim of this is to reduce the amount of variation when picking and to reduce as much operator travel time as possible. Each wave will have consistent routing, loading and planned departure times of shipping vehicles, and it will assign staff to each wave.
Drilling a bit deeper, there are even different ways to pack within this method of picking. With fixed-wave picking, all the items in that wave must be picked before they are packed. With dynamic-wave packing, orders can be packed as they’re picked but you’ll need an operator to make sure all orders are being completed.
Should you use wave picking?
Use this method if you have a large number of SKUs and a WMS to organise the workflow for the day for you. Don’t use this method if you don’t have a WMS or if you don’t know how to program to generate the waves that are most needed by your business.
Zone Picking
Zone picking takes speed and efficiency to a new level. Customer orders are combined into a master batch that’s been picked by multiple pickers in their dedicated zones.
If you utilise this method, then you’ll have inventory pickers that forward their items onto a sorting area where the masterbatch is then broken down into specific customer orders.
You’ll most likely be using this method if you have a lot of customer orders for a range of different SKUs. If you find yourself in need of reducing travel time while also being overwhelmed with inventory transactions, this method is definitely for you.
Should you use wave picking?
Use this method if you have a distribution centre with a large range of SKUs that are fast moving products, and if you have the required inventory pickers for the number of zones you need. Don’t use this method if you don’t have the required space to have a central picking area or if you want to assign responsibility for picking errors.
How to Know When To Change Your Picking Method
As deadlines creep up and new orders continue to gush in, it’s easy to become overwhelmed and jump into a solution without thinking. The problem, though, is that there are many variations of picking and some businesses even combine a range of different techniques. For example:
- Zone and Batch Picking
- Zone and Wave Picking
- Zone, Batch and Wave Picking
- Discrete Order Picking and Batch Picking, to name a few.
Only you can know when a picking method is no longer suitable for your business, but what is important is understanding when the right time to switch things up is. We’ve also written a guide on how you can make your pick and pack process faster so this might be a great place to start before you overhaul everything.
But we do have a few things you should consider before you change the way you operate:
1. Make sure your new picking method suits your demand
There could be nothing worse for a business to go through the process of switching from discrete picking to zone picking only to find that customer orders come in dribs and drabs leaving some pickers without anything to do.
You need to understand your current picking methods’ shortfalls and why it’s not meeting your needs. Then you can research into which picking method is the best for you at that point in time.
2. Make sure you have the technological requirements for a picking method
As mentioned above, some picking methods require the assistance of software applications to do the brunt of the work and calculations. If you’re running a business, the last thing you’ll have time to do is sort out your orders by item, allocate pickers to each zone, all while filtering out waves throughout the day.
Your time is better spent doing other things, but just make sure you have the right technology in place and the right know-how to set it up.
3. Make sure you have the right amount of space and resources to change your picking method
Some picking methods require more space than others, so this is definitely something you’ll need to consider before you change. Further, when you’re a growing business you may not have 5-10 inventory pickers that you can allocate to each zone.
If you’re light on resources, consider the method that will give you the best results for your current resources.
4. Stay agile
Picking is something that has a direct impact on the satisfaction of your customers. It’s worth putting a lot of thought into how you can improve it regularly so that you don’t get stuck in inefficient ways of operating.
When running a business, it’s easy to get caught up in the fun things (like creating Old Spice memes), but you need to constantly review how your current processes are working for you and your customers. If nothing is wrong? Great! Don’t change anything. But if there is something wrong, make sure your business is agile enough to fix the root cause of the problem.
We hope you found this post enlightening. We’d love to hear how you pick and pack. Was there a method we left out in this post? Let us know in the comments below.
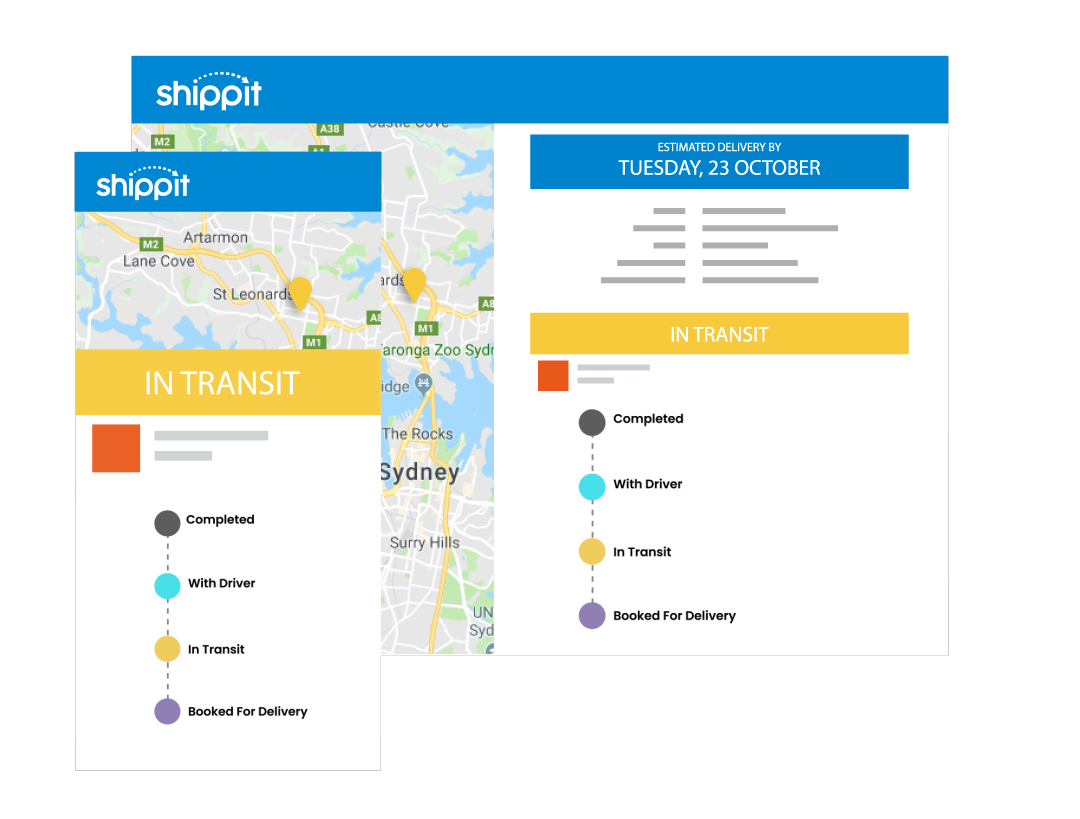